Due to the fact that it is a guided vehicle, Skylark L has an onboard control system and thrust vector control system, as well as a roll control system. During flight, the onboard control system operates guidance algorithms to correct the flight course when any disturbance factors occur. Control of the launch vehicle at the boost phase of launch along pitch and yaw axes is ensured by the deviation of the combustion chamber of the main engine. Control of the launch vehicle at the boost phase of launch along the roll axis and control of the pitch and yaw at the coast stage of launch is ensured by the roll control system.
advantage
specifications
- Length 11.65 m
- Diameter 0.7 m
- Lift-off mass 2,466 kg
- Payload mass 50 kg
- Propellant HTP / KEROSENE
- Apogee altitude 102 km
- Time to apogee (from launch) 225 s
- Max G-load 3.7 G
- Maximum velocity 950 m/s (MACH 3.5)
engine
Regeneratively cooled liquid rocket engine using a pressure fed system.
Nominal thrust of the main engine:
- 31kN above sea level
- 35kN in vacuum
Nominal specific impulse:
- 229 seconds above sea level
- 272 seconds in vacuum
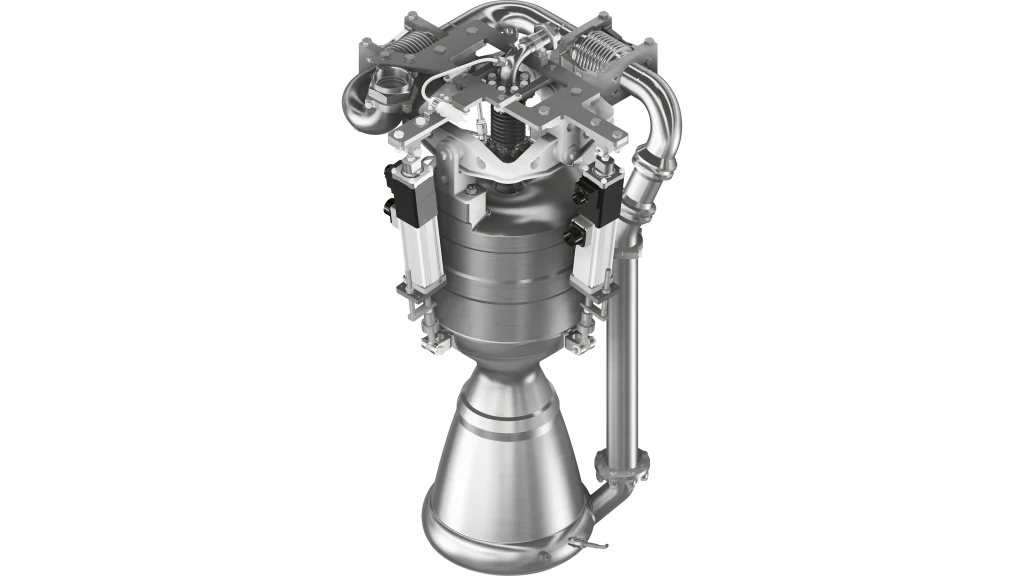
materials
Skyrora utilise high grade materials, namely polymers such as epoxy, vinyl ester, polyester resins and fibres, glass, carbon, and aramid in order to provide the best physical and mechanical properties of composite parts to maintain a high standard of quality that is essential within the aerospace industry.
Flight profile
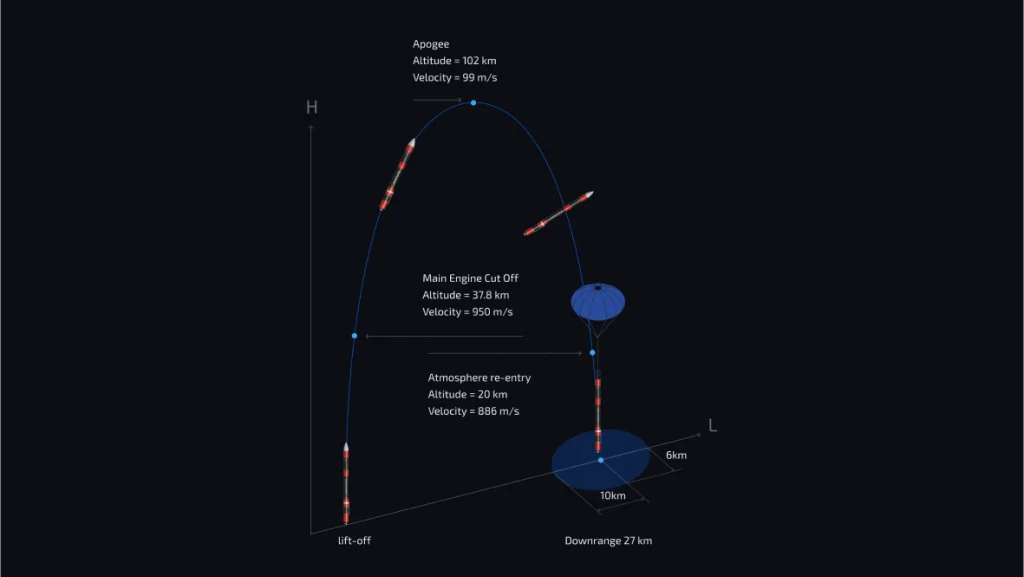
Launch Pad
Every part that makes up the launch system has been developed by Skyrora, with most of these parts in operation after undergoing successful testing. Remaining parts are currently in the final stages of testing.
PAYLOAD MODULE
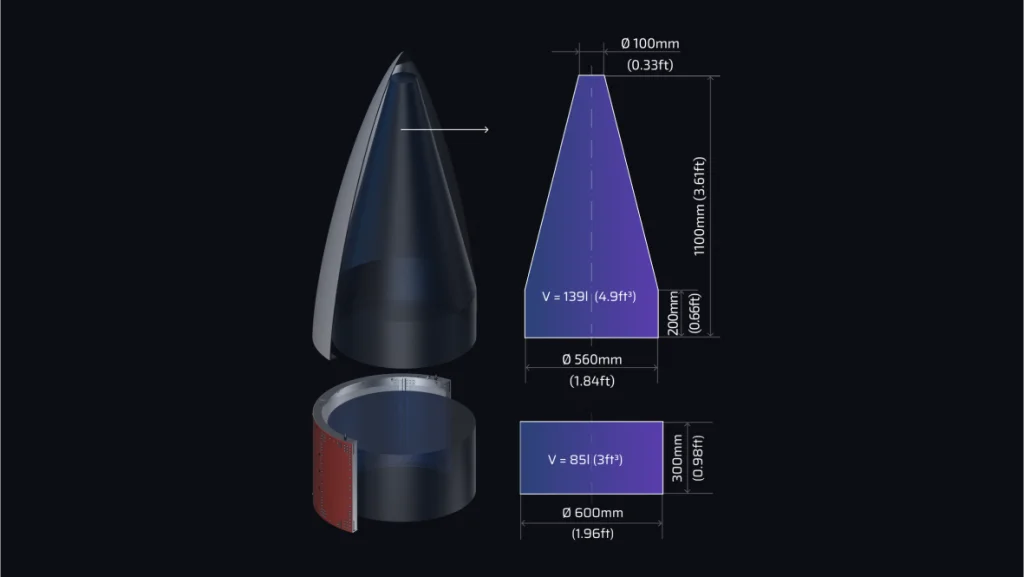